my 2 cents, weil hier einige Male verschiedene Dinge durcheinander geworfen wurden:
(Korrekturen werden gerne entgegengenommen, kleine Fehler oder Unzulaenglichkeiten sind bestimmt enthalten)Auch wenn Elon von 'single cast' twittert, bezweifle dass das ein Guss ist. Titaniumguesse sind schwierig wegen der hohen Temperatur. Es wird ein Schmiedeteil sein, das ist absoluter Industriestandard und verhaeltnismaessig leicht und guenstig zu beschaffen. Schmiedeteile werden, wie alle Metallteile, irgendwann aus einer Schmelze erzeugt - nur danach geschmiedet. Schmieden ist ein (idR heisser) Umformprozess, bei dem die Werkstoffeigenschaften verbessert werden. Das ist der Grund, warum Schmiedeteile bis heute verwendet werden. Bleche werden gewalzt, was eigentlich ebenfalls ein Schmiedeprozess ist, sprachlich nur anders dargestellt.
Abhaengig von der Art und Geometrie des Umformens sind diese Festigkeitssteigerungen nicht in alle Achsen vorhanden - Bleche zB haben geringere Festigkeiten in der Hochachse, in Abhaengigkeit vom Lastfall muss das
lokal ueberprueft werden.
Andere Fuegeverfahren wie 3D Druck oder Schweissen erreichen nicht diese Festigkeiten. 3D Druck gehoert zu den Sinterverfahren, ebenso wie das Toepfern. Sinterverfahren koennen sehr feste Stoffe erzeugen, einige Verbindungen (Hochfeste halbkeramische Schneiden zB. aus
Carbide koennen nur durch Sintern erzeugt werden - hat dann aber nichts mehr mit 3D Druck zu tun
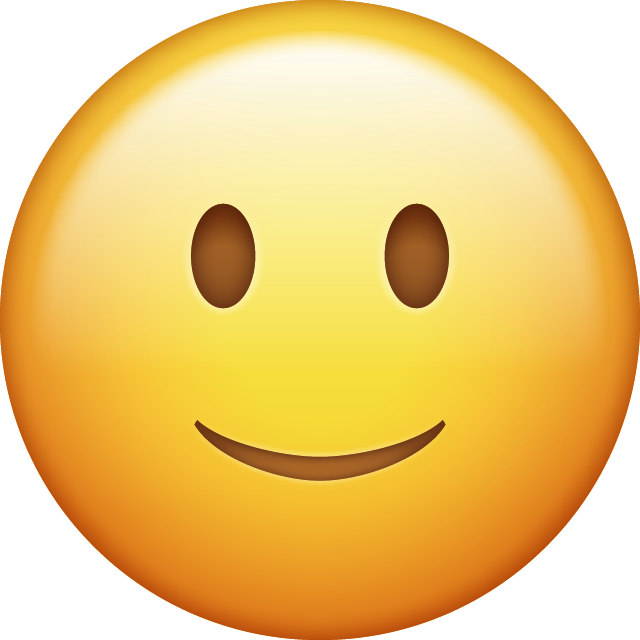
ZB wird in der Chemischen Industrie im Hochdruckbereich (zB. Wachse,
PE-Anlagen) wird gar nichts mehr geschweisst, alle Rohre, Reaktoren, Waermetauscher etc sind ausschliesslich geschraubte Schmiedeteile (welche RIESIG sein koennen -> youtube).
Es gibt auch zahlreiche Trennmoeglichkei ten.
- verbrennenden 'Baustellen'-Trennschneiden mittels Sauerstofflanze oder noch viel rabiatere Methoden ('Carbon Arc Gouging') zu 'bessren' Trennmethoden
- thermische Schneiden (Laser-, Plasma- Acetylenschneiden sind nur drei unterschiedliche Methoden, wie das Material aufgeschmolzen wird. Bei allen blaesst ein Gasjet das Schmelzgut heraus, wodurch der Schnitt entsteht). Laser ist nur deshalb gut weil der Laser sehr fein fokusiert werden kann, weshalb erst sehr feine Strukturen aus sehr duennen Blechen geschnitten werden koennen. Das wurde davor mit einer Schneide geschnitten oder gestanzt.
- kaltes Schneiden mittels Wasser erzeugt gleiche (Plasma/Acetylen) oder schlechtere (Laser) Schnittqualitaeten, bringt dafuer aber keinerlei Waerme ein - viele Legierungen sind waermeempfindlich. Andere schmelzen einfach nicht (Karbide, Salze, Steine).
-
Zerspanen (Fraesen, Drehen) ist ein eigenes, riesiges Feld. es gibt Staehle die gezielt auf gute Bearbeitbarkeit gemacht wurden (ich glaube Schwefel als Legierungselement erzeugt kurze Spaene) Abhaengig von der 'Maschinbarkeit' von StahSchneidgeschwindigkeit wird ebenfalls unterschieden. Im Englischen wird, teilweise ueberdeckend (hab das nach all den Jahren selbst noch nicht herausgefunden) von
Machining, Cutting, Milling, Drilling, Lathing etc. geredet - der Unterschied liegt oft eher im jeweiligen Anwendungsfall als der anwendeten Maschine (=>
SpaceX Machining Workshop).
Ergaenzung zu Oberflaechenverguetung: (Kann das Aussehen unabhaengig vom Fertigungsverfahren wieder deutlich aendern)
Nach dem Bearbeiten wird oft noch die Oberflaeche verguetet. Abhaengig vom vorangegangenen Bearbeitungsgrad oder spaeteren Anwendungsfall:
- Haerteverfahren mittels Gluehen und evt. nachfolgendem Abschrecken mittels Luft, Wasser, Oel oder auch stickstoffhaltigen Fluessigkeiten
- Beizen und Passivieren, nach Waermeeinfluessen wie Schweissen. Mittels Saeuren werden Verunreinigungen weggeaetzt sowie eine gleichmaessige Oberflaeche erzeugt, die beim Passivieren (idR einfaches Aussetzen an sauberer Umgebungsluft) dann eine gleichmaessige, alles bedeckende Oxidschicht aufbaut (Chromoxid bei Edelstaehlen zB).
- Strahlen mittels Sand, Trockeneis, Keramik oder Glaskugeln, Metallischen Koerpern, etc. In den letzten Jahre an Bedeutung gewonnen, da durch dieses 'Mikropitting' Druckspannungen in der Oberflaeche erzeugt werden, insbesondere in der Passivschicht, wodurch Rissbildung verringert wird. Dies erhoeht die Korrosionsbestaendigkeit, die Dauerfestigkeit bei Schwingungen etc und die Temperaturschockbestaendigkeit.
Aus meiner Sicht werden diese Gridfins aus einem massiven Schmiedeteil herausgearbeitet, mittels Multi-Achsen Fraese. Wenn SpaceX von teuer redet, dann ist das vermutlich eher im Verhaeltnis zu sehen. Aluminium ist viel leichter zu bearbeiten (weicher, weniger entzuendlich!) und deutlich guenstiger. Ich kenne Preise von ca. 40-60 Eur/kg fuer ein Schmiedeteil bei Titan, Alu dagegen ist weniger als 5 Eur/kg. Ein bearbeitetes Teil verdoppelt sich gerne mal im Preis, abhaengig wie hoch der Zerspannungsgrad ist.
Die Abmasse der Alu-Gridfins ist ca. 1250x1550mm (
5x4 ft) mit einer angenommenen Dicke von 100mm. Die Titan-Gridfins sind etwas groesser, ich nehme mal 1250x1700x100mm an, der Rohling wiegt dann ca. 1000kg, entspricht 60TEUR! Der Alu-Rohling, etwas kleiner, wiegt die Haelfte (geringere Dichte!) und kostet nur 2.5TEUR. Vor dem mechanischen Bearbeiten, was bei Alu ebenfalls viel einfacher ist.
Fuer Luft- und Raumfaehrtanwendung ist das eigentlich immer noch billig, aber nun wird glaub ich etwas klarer warum fuer SpaceX die Titan-Gridfins so viel teurer sind.